PART II: RUNNING A FRAC SAND MINE
Operating a frac sand mine seems so simple. After all, the process is straightforward, predictable and linear:
-
- SAND IN GROUND
- Dig up sand and dirt from ground
- Wash dirt
- Get sand out of dirt
- Let sand decant
- Dry sand
- Segregate sand by mesh size
- Load sand in customer truck
- Truck takes sand to frac site where sand goes back underground
- Get paid for sand
- REPEAT
If that sounds dull, it would be, if it were that simple. Fortunately, there are mind-stimulating challenges along the way, so there’s rarely a dull moment when we’re moving 2,000 tons of sand here at our Blaine Facility every day of the week.
Finding the Right Folks
That’s why, when we were opening this plant, we started by finding great people who were up to the challenge. Our favorite hires are people who arrive ready to learn, to work and to be a team.
Those are the people we hired for the Blaine operation as we ramp up to our total workforce of 80. We looked for someone with the right spirit, who we can teach. Someone who comes in excited about their job and their day will do everything they can to keep things running smoothly. And people who communicate—they understand what it means to be a team and to have each other’s back.
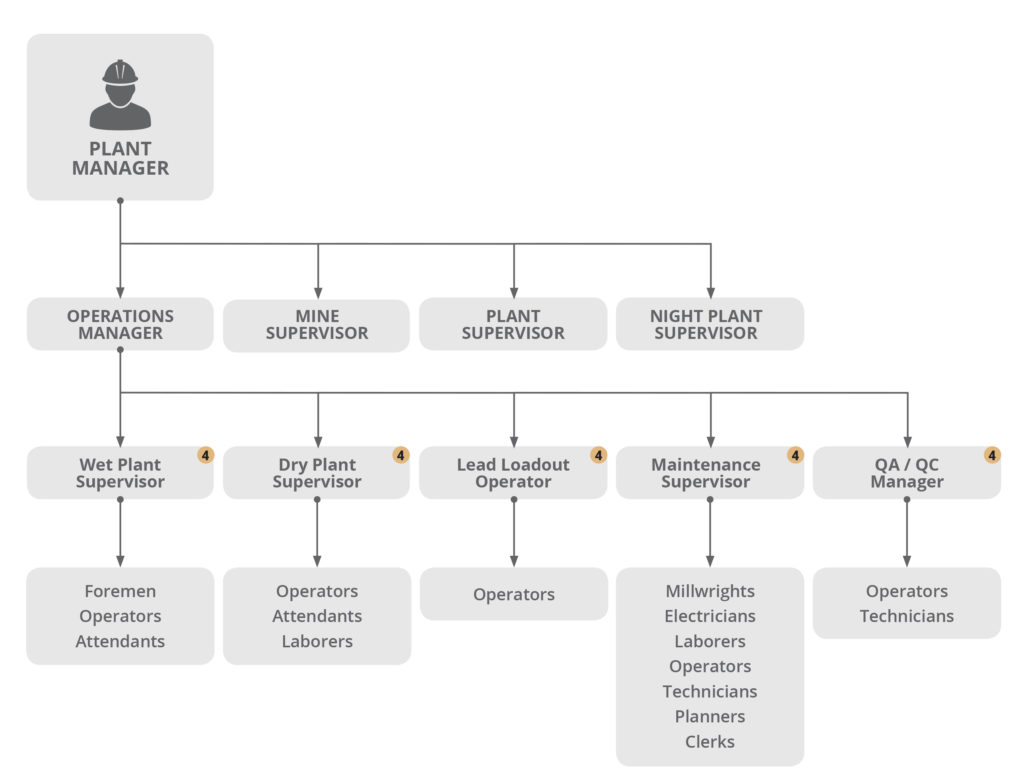
Basic Organization Chart at a typical frac sand site
Cliché Alert: Communication is Key
Communication is why we start and end every 12-hour shift with a meeting, 5:45 a.m. for the 6:00 a.m. shift and 5:45 p.m. for the 6:00 p.m. shift. Everyone comes in 15 minutes early and leaves 15 minutes after their shift. In that information-packed quarter hour overlap, the people leaving update the ones coming on about any issues the incoming crew needs to be aware of. We also have a daily operations meeting at 9:00 a.m.
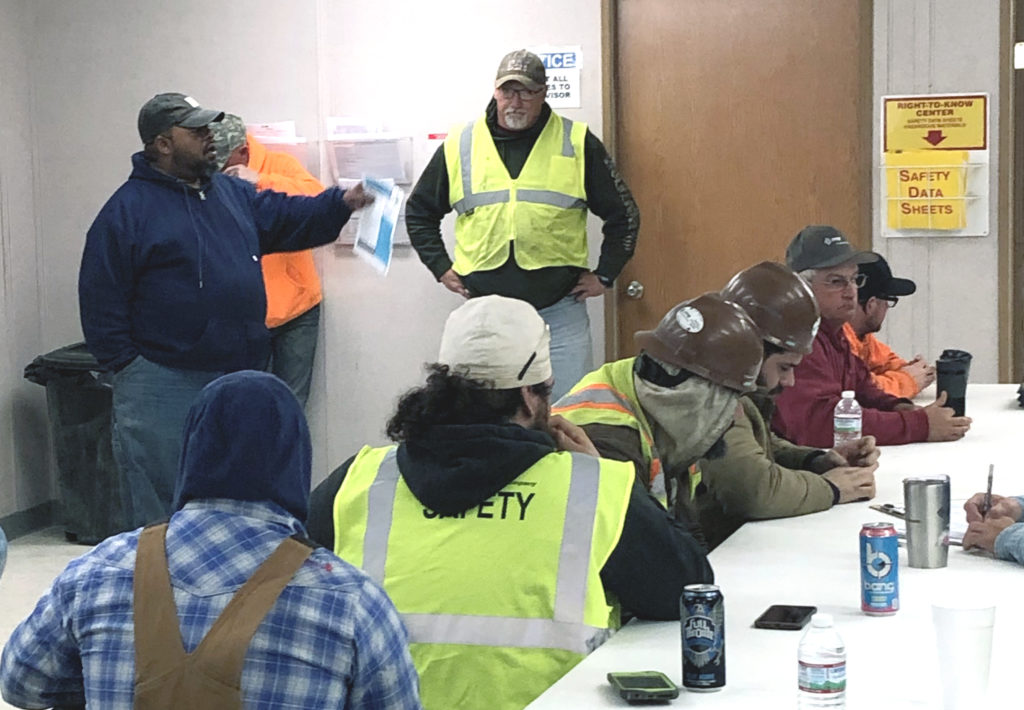
Start and end every 12-hour shift with a meeting for better communication.
Hours can be long, but we’ve worked it to where days off are long also. Our people work seven days on-seven days off. We managers—well, we’re available 24/7, especially at the beginning.
As simple as that opening list looks, each stage (and there are more stages, that list is just the highlights—we’ll cover more stages in depth in future blog posts) involves three things: Sand, equipment and people. Most steps follow someone else’s step and precede another’s. If you do your part right, you make the next person’s job easier.
Cross-training Our Team
That kind of thinking is why we cross-train everyone. For one thing, it helps when there’s an issue at a particular place—we can run a couple of extra people there to get things ironed out.
Second, it helps each person know exactly what the next person in line is expecting and needing to keep the sand flowing. And they know how important it is to keep work flowing so as not to let work back up on the person before them.
We think of it this way—there are internal customers (coworkers in the adjacent stages) as well as external customers. The best days are when we fully please both.
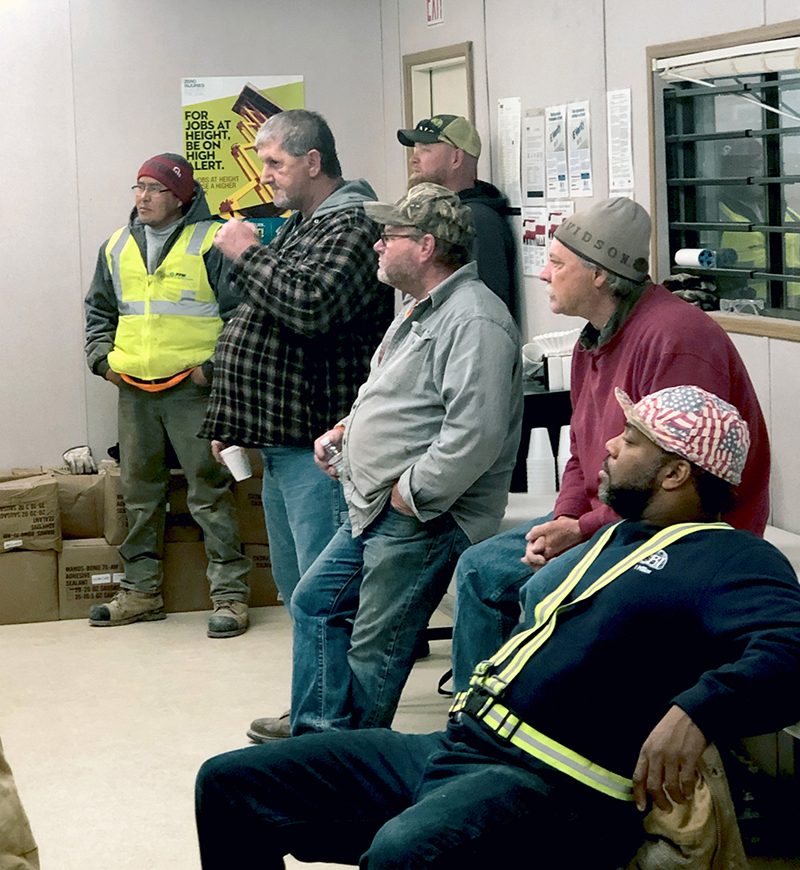
Team listening to input to improve operations
Customer-Focused
All this comes together in meeting our biggest goal, which is to respect our external customers’ time. We want to get those trucks in and out in less than 10 minutes, so they can get back on the road and onto productive time. We say 10 minutes, but we really like 3:30-3:40.
We think that kind of service brings customers back to us over and over on the hundreds of frac sand loads each well requires. (And according to recent market analysis, average proppant volume in Oklahoma is upwards of 5,750 tons/well.)
As you may have noticed, I love my job. Yes, it’s a J. O. B., but it’s way more than that for me, and for my people. I’ve always been into race cars, motorcycles, racing in general—so I do love getting to work with the shiny new equipment in a new mine. I do. But I love building and working with teams of people even more.
I want the people to love their jobs as much as I do. I always take real input from people at team meetings. If they’re actively solving issues, then they’re fully invested in the situation and I know I can trust them all along the way.
Then they’re asking, “How much did we ship,” and “What was our quality?” They’re wanting those better numbers just like management does.
Here’s the Big Picture…
Only one percent of the people in the world are miners—but the other 99 percent depend on what we do. That one percent includes the rest of the oil and gas industry as well as us.
Big responsibility? Yep. But it means what we’re doing is important.
And that makes this so much more than a J. O. B.
Next Time:
Now that we’ve highlighted how to find frac sand and what it takes to open and run a mine; we’ll dig deeper into the process of manufacturing sand. Up first: how we make sand in spec for hydraulic fracturing.
We Want To Hear From You!
Have questions? Comments? We’d love to hear from you! We want to get to know our neighbors, so please send us your questions on the form below. We’ll share your questions with our answers on social media each week! Follow our story: #InsideFracSand
This Month’s Contributor
Michael Simmons
Plant Manager, Blaine Facility
As a Frac Sand Plant Manager, Michael oversees the day-to-day operations at our Blaine Facility. From evaluating and implementing plant efficiencies to developing an effective team, his expertise has been crucial in the start up of our newest plant in Fay, Oklahoma. Hailing from Memphis, TN, Michael has over 20 years of operation management experience, an associate degree in Math and Chemistry from Jackson State Community College, and is a certified Lean Six Sigma Green Belt.